Introduction: How to Get Started With Precious Metal Clay Jewelry
In this project I am documenting my first experiments with precious metal clay jewelry and am going to share some of the tips and tricks and tricks I have learnt along the way as well as some of the things I've realized do not work well, which I learnt the hard way!
This project was a challenge I set for myself to learn some new skills and hopefully I can help you learn some as well.
What is PMC?
Precious Metal Clay is a material made up of water, an organic binding agent to hold it together and very small particles of a precious metal such as Gold, Bronze, Copper or as I have used in this project, Silver. It is a very versatile material that can be worked and sculpted just like regular or polymer clay. However, due to the composition of PMC it is prone to drying out easily, so you need to be careful to keep it hydrated or in an airtight container.
In this project I am making a ring with PMC but the techniques can be used to make any sort of jewelry.
Step 1: Tools and Materials
This project can be done easily with just precious metal clay and a method to fire it. For silver clay, and copper clay, it can be quite easily fired using a hand torch. However, bronze or gold clay may require the use of a kiln. Check the specifications for the specific clay you are using for best results.
There are a variety of great websites that have a large selection of tools and materials for working with metal clay, in the UK the retailer I have used is Metal Clay Ltd. - http://www.metalclay.co.uk/ I have had great experience with them so far. Another retailer I have seen good reviews for online is Cooksongold https://www.cooksongold.com/ but there are lots out there so if you have a look and find one near you!
In this project the materials and tools I have used are as follows:
Material:
Art Clay Silver 20g low fire clay
Tools:
Silicone work mat
Glass surface
Acrylic roller and spacers
Badger balm
Leather punch cutters
Straight blade
A spray bottle full of water
Pencil and eraser
Selection of burnishers
Wooden ring mandrel and ring size chart
Sanding sponges
Needle files
Handheld gas torch
Step 2: Prep Your Work Surface
I have found that PMC sticks to pretty much everything if you do not prep your surfaces and tools properly!
Something that has been really good at preventing this is Badger Balm, you can rub a bit of it over your work surface, hands and any tools that will be in contact with the wet clay and it works very well at stopping the clay from sticking.
Step 3: Rolling Out the Clay
Start by rolling the clay together into a ball, and then start to elongate it into a thin cylinder. How long and wide this cylinder of clay is will depend on the piece you intend to make.
Then place this cylinder between your spacers so that you can roll the clay to a uniform thickness using your roller. In most tutorials I have seen for working with precious metal clay, they use the thickness with respect to how many playing cards thick it is, this is done to make it easy to roll out to a desired thickness consistently. I used some plastic spacers for this ring, which were about 5 cards thick. Whether you have plastic spacers like me, or are using playing cards, either will work great.
You can then begin cutting out any shapes you will need for your project, but don't forget to put some balm on any cutters you are using to stop the clay sticking!
Step 4: Cutting the Shapes
PMC Is great at making really organic looking pieces as you can sculpt it and treat it just like regular clay, so you really don't need any tools at all other than your hands, a work surface and something to stop it sticking. You can make all sorts of cool designs by just sculpting something allowing it to dry and firing it. Use your imagination and make something you can be proud of!
In this piece I wanted to make a more specified design and was not aiming for a more organic or abstract final piece so I used some leather punches I had to cut some shapes out of the clay to make it more uniform.
Make sure that any clay you are not using, or excess which has been cut off, is wrapped in something like plastic wrap or tucked in a container with a damp cloth or sponge so that it doesn't dry out. Although it is possible to re-hydrate the clay and use it again if it dries out, if it has fully dried the moisture may have difficulty penetrating into the pieces of clay and it may just be more difficult to get it back to the original consistency.
Another tip is any small bits of clay that may fall off during the process of making your pieces, or any powder that comes off when you sand an un-fired piece, you want to save all of those bits as they can be used to make a paste to join pieces, or if you get enough, can be made back into clay!
Step 5: Joining the Clay
Here, I am using a little bit of the dried clay powder and mixing it with a bit of water to form a paste, and then brushing that paste on to each piece of clay that I was pressing together when I was forming the ring around my mandrel.
Make sure that if you are joining pieces of wet clay, that you apply enough pressure to the join to make sure they will be solid as the piece is fired, if you are worried reinforce the seam with some paste or a little more wet clay, which you can then smooth out with a wet brush.
If you are trying to use paste to stick two pieces of clay that have already dried, it is easy to do, however you will want to make sure both pieces you are going to join are quite flat and have a large contact surface. Then simply brush the paste on both pieces, and apply pressure to allow them to join.
For the split shank ring design I have made, it was really important to get all of the pieces which made up the band and the circular face, so I made sure each piece was still wet and added paste to the joins, which then were firmly pressed together until they became one solid piece.
When sizing a ring in PMC remember that the material will shrink when fired as the binders burn off and while the metal is sintered. Each clay will shrink slightly differently, the art clay silver I used is about an 8-9% shrinkage so to compensate for that your need to size your ring accordingly, about 1.5 US sizes or 3 Japanese sizes bigger I have found works well but it depends on the thickness of your band. For the ring I made, I wanted the final size to be a 7.5 US or 15 Japan and so I sized the ring before firing at a 9 US or 18 Japan.
Step 6: (Do Not Be Afraid To) Change the Plan!
I was not really happy with the form the ring was taking and was worried about the security of some of the joins I made between the clay pieces (this is actually the second ring I have tried to make, when the first was fired, the clay had not joined well enough and it unfortunately broke). In order to improve the structural integrity and change the shape a bit, I added some additional clay over the areas I was concerned about. Which is another great aspect of this material, nothing is set in stone until you've fired it!
I used the clay to make a circle shaped plate with a bit of a lip to put on the front of the band. While the clay is wet and you are forming it together you can use a brush with a little water on it to brush down the surface and smooth it out to save yourself sanding later
If you wish to set a stone in your piece, a good way to do so is to make a small ball of clay, and flatten it into a slight cylinder and use some paste to stick it to your piece. Or if you have a syringe of clay, make a small coil of clay about the diameter of the stone on the piece, once you have your setting, then press the stone into that clay until they clay comes up to the widest point of the stone. When the piece is fired, It will shrink slightly, securing the stone in place. Be very careful when firing with a stone.
Step 7: Final Detailing Before Firing
Once you have the main form you would like together, allow it to fully dry and you can begin doing some finishing work and final detailing before you fire. It will be a lot easier to sand or file your piece now than it will be once you fire, so take advantage of that to save yourself some work later! File the band to shape and sand the piece to be smooth and uniform. However, as it is still just dried clay and not fired, your piece will still be very brittle and fragile so handle it with care.
Once the clay is fully dried it should be about leather hard, and this will allow you to carve some detail and engraving into the piece if you wish to do so.
I just used a very sharp H pencil to draw the design which I wished to engrave, and then once I had it the way I liked, I gently began to carve the design into the piece using the sharp burnisher, and the fine ball burnishers to give it dimension.
I did a lot of the finishing work for the ring while it was on the mandrel, as that supported the ring and allowed me to maneuver it and do fine detail work without worrying about breaking it. Be very careful through all of this stage as is you drop the ring or bang it on something it can easily break, which is extremely frustrating, but you can attempt to fix with paste.
Once you are happy with the design, go ahead and fire to make it once solid piece of metal!
Step 8: Firing the Clay
There are two different stages to firing PMC.
To start, you will want to place the piece you are firing on a heat resistant surface such as a kiln brick or elevated wire mesh. Then, set your torch to a high flame and begin to gently heat the piece from one side to the other.
At the beginning you will see the piece catch fire as the organic binders of the clay burn away, once this has finished the piece will continue to heat and will allow the metal to begin sintering.
Step 9: Sintering the Metal and Quenching
Once the organic binders have been burnt off, you will want to keep gradually heating the piece until it begins to glow a light salmon colour. Then, keep the piece at this light salmon colour for at least 2 minutes, possibly longer depending on the size of the piece.
Be careful not to get the piece too hot or you risk burning the metal, if the piece begins to look liquid or silver in colour the metal is getting too hot and can result in pitting or cracking of the piece. After 2 minutes (or longer) at the correct temperature, you can quench the piece in water or allow it to slowly cool to room temperature. If you have set any stones or cabochons in your piece do not quench it, allow it to cool gradually, and be very careful during heating to avoid cracking the stone.
Step 10: Finishing Work
Now your piece will be solid metal and you can file and sand it as you wish to finish it to your liking.
When your piece comes out of the water or has cooled naturally, it may have a white coating over it, this is natural it is just residue from the binders being burnt off or oxidation of the silver, just brush it down with a steel wire brush to remove this residue and begin to polish your piece!
If you are filing or sanding your piece make sure to go to progressively higher grits and remove all the scratches from the previous grit in order to assure a good finish. Then simply hit it with some silver polish and you are good to go!
For my piece, I really wanted to increase the contrast to highlight the engraving, so I patinaed my piece using Liver of Sulphur and then polished the high spots leaving the recesses still dark.
Step 11: Admire Your Work
Be proud of what you've made and enjoy your new set of skills!
Hopefully this Instructable has helped to give you a bit of advice and a diverse set of skills you can use to make any sort of jewelry you like! Making a pendant will be a bit easier than a ring as you do not need to worry about shrinkage of the material as much but I encourage you to use these skills to make something creative and I would love to see what you come up with!
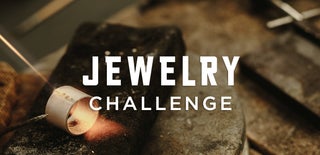
First Prize in the
Jewelry Challenge