The use of X-ray technology in PCB inspection has gained popularity over time. Inspection plays a significant role in PCB manufacturing. There are several methods of inspecting a printed circuit board. The X-ray inspection is reliable and efficient. Also, X-ray technology is widely used across various industries. From the aerospace industry to medical, X-ray inspection is a good tool for detecting errors.
However, it is very prevalent in the PCB industry. X-rays are a good method to test the functionality and quality of a circuit board. Also, X-ray quality control and inspection is high beneficial to PCB manufacturers and users. This article, we discuss the specific benefits of X-ray and how it works.
What is PCB X-ray Inspection?
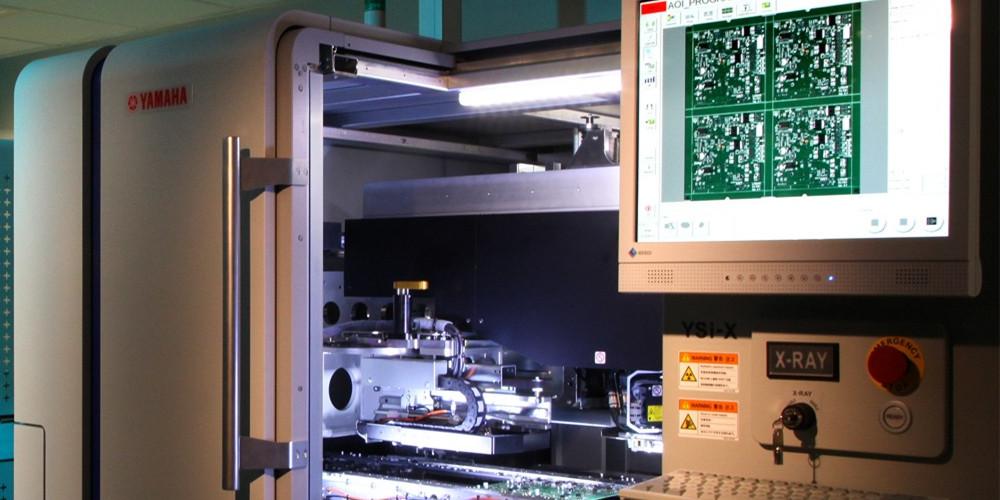
The PCB X-ray inspection is a reliable method of detecting defects in circuit boards. Also known as automated X-ray inspection, PCB X-ray uses electromagnetic waves and short wavelengths to detect any PCB defect. This inspection method utilizes X-ray to inspect features which may be hidden from view. Also, it is a widely used method to detect invisible defects associated with BGAs and ICs in PCBS.
X-ray is the main scanning source in this inspection system. Also, the X-ray detects large cracks and voids. Just like automatic optical inspection, X-ray captures images. The X-ray machine penetrates the PCB and discovers defects in it. Also, the penetrating effect of X-ray makes it ideal for use in PCB manufacturing. This effect enables manufacturers to easily detect hidden features and faults in the circuit board.
Also, the X-ray inspection can detect hidden defects like missing electrical components, shorts, and misalignment. The principle of X-ray devices is the X-ray projection microscope. This starts with the production of X-ray. Also, the X-ray has to launch tube to pass through the inspected circuit boards.
Projection is produced on detectors since various materials feature different X-ray absorption. X-rays can generate light that can penetrate the PCB. Also, the light then reveals an image with various density and thickness. The quality of the image indicates the quality of the PCB.
Some factors determine the penetrating power of the X-ray machine. Also, these factors include material density, the X-ray energy, and the nuclear change of the material. X ray easily spots soldering flaws during the manufacturing stage of a PCB. Also, X-ray inspection helps to detect multiple defects. These defects can be either evident or seen. X-ray doesn’t just detect bad solder joints, but also detect the area that caused the defect.
How the X-ray Inspection System Works
It is crucial to understand how this inspection system works. PCB materials absorb X-rays based on their density, thickness, and atomic number. Thick PCB materials tend to absorb more X-rays than lighter materials. Also, heavy materials look darker in their images. Lighter materials are transparent to the radiation. Solder joints comprises heavy materials. Therefore, they appear darker on images.
During inspection, the PCB manufacturer places the component between the detection component and X-ray machine. The X-ray inspection system features a fixture that enables engineers to hold and manipulate the subject. Therefore, the engineer can evaluate the subject from a different area. As the X-ray machine goes through the subject, the intensity and quality of the rays will reduce. Also, this is a result of the changing density in the test subject.
This results in the different shades of dark and light areas on the detection surface. For example, a crevice or crack in a solder ball will display easily in an X-ray. This is because the solder features a higher density compared to the air in the crevice. Therefore, the minimized density will weaken the X-rays intensity.
Furthermore, the X-ray device comprises a detector, an X-ray tube, and a sample operation platform.
- The detector is capable of capturing X-rays that pass through the sample. Then, it will transform these X-rays into a projection users can understand.
- The X-ray tube produces X-rays. This tube features closed tube and open tube. The correspondence to the inspection device’s resolution determines the type used. Delicate details will become more visible as the resolution rises.
- The sample platform inspects the sample from different magnification and angles. The user can examine the sample via an oblique angle.
Classifications of X-ray Machine

There are two categories in the PCB X-ray inspection system. These categories are two dimensional system 2D and the three dimensional system 3D.
2D system
A 2D system reveals the 2D pictures from both sides of the circuit board simultaneously. Therefore, this creates an image of the components of the PCB. Also, the 2D system produces X-rays at a single point. The X-rays goes through the circuit board. This system is ideal for single-sided boards. Also, it suitable where accuracy is crucial. The 2D system integrates the traditional concept of an X-ray used in medical systems.
3D system
The 3D x-ray inspection system can create 3D images of a circuit board by creating a series of 2D cross-sections. Also, it works in a similar way with CT scan. 3D X-rays can perform well using the laminography method. This method uses cross-sections to create a particular part of an area.
PCB manufacturers integrate this system for complex double-sided boards. The 3D x-ray inspection requires two crucial components. Also, these components are the X-ray source and the detector. The detector goes through a 180-degree circular movement.
The 3D X-ray transmission helps to produce images of different cross-sections. It achieves this by reconstructing and combining series of 2D images. Also, the 3D x-ray concentrates on a single feature. Therefore, it blurs other components like soldering joints. This enables you to evaluate a particular component of interest at a time.
Choosing the best system for your X-ray inspection requires the consideration of some factors. The quantity of the inspected product and the amount of time available will determine the type of system to opt for.
Benefits of PCB X-ray Inspection Method
X-ray offers a lot of benefits. Generally, X-rays are capable of detecting hidden defects. Therefore, they are more reliable than some PCB inspection methods.
Checks Errors in landing patterns
During PCB assembly, several mistakes occur. The landing pattern of certain elements on the PCB is one of these mistakes. If the components assembled on the PCB aren’t part of the components in the library of SMD components, it can get the landing pattern wrongly.
The PCB designer needs to generate a schematic of the recently introduced component on the PCB. When this schematic isn’t available, mistakes might occur in the landing pattern. Also, this mistake may be difficult for visual inspection to detect. A PCB X-ray machine makes it easier to detect a wrong landing pattern.
Sees through BGAs
Ball grid array allows the production of small devices. Also, it allows installment of tiny components on the circuit board. However, BGAs can be difficult to inspect since components are tightly packed on the PCB. This doesn’t allow much space between installed components. Also, the X-ray inspection equipment penetrates the BGA assembly easily and detects any defect.
Identifies several potential problems
This inspection method can help you detect possible issues like lifted leads and missing components. Also, X-ray helps to optimize PCB manufacturing stage to produce functional PCBs.
Allows image comparison
X-ray imaging helps to compare several images of the same product. Therefore, this helps you to detect any changes made in a production run. Also, it allows you to compare between products at different stages in their life cycle.
Safer and more efficient
X-ray imaging is safe and reliable PCB inspection method. Also, this PCB inspection method is faster. It doesn’t require the inspector to send for analysis.
What are the Common Defects PCB X-ray Inspection Technology Detects?
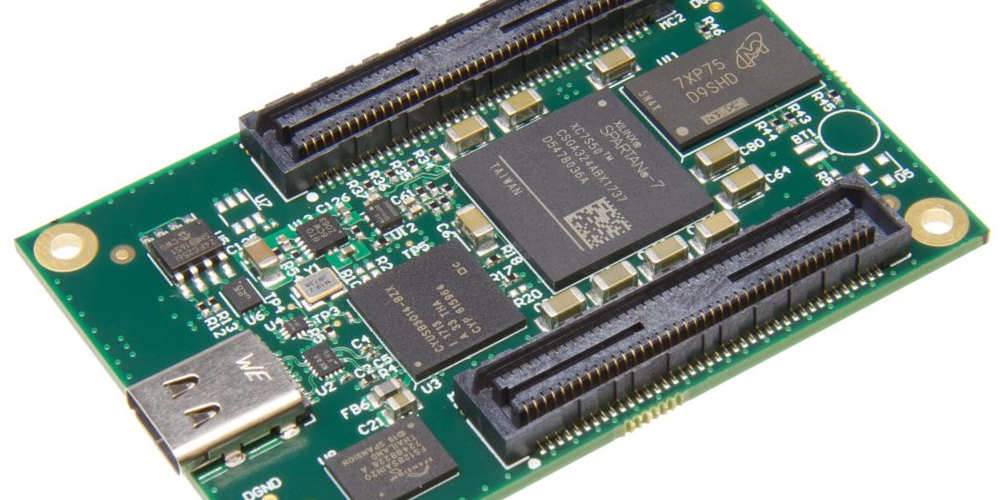
The X-ray inspection technology detects some defects that are invisible and hidden. This capability is what distinguishes X-ray inspections systems from other inspection methods. In X-ray images of a circuit board, the metal appears dark. Other materials like ceramics and glass are transparent. Therefore, inspectors can view different metallic parts on a circuit board.
Also, the X-ray inspection equipment will allow inspectors to view several qualities of a PCB.
Solder voids
There is formation of solder voids when flux or gas entraps while soldering. This often occurs when water contaminates the solder paste. Also, voids reduce heat conductivity at the solder joint. This can reduce reliability and result in physical defects. The X-ray images reveal solder voids problems.
Pin hole fills
This is one of the common defects X-ray inspection technology detects. Pin-hole fill is a common defect in PCBs. The X-ray inspection systems identify these defects. Also, these systems use coordinate measurements to quantify the amount of missing fill.
Solder bridges
Solder bridges will occur when solder joints stay too close. Other components hide solder problems. Therefore, this makes it difficult to locate them with optical inspections. However, X-rays can detect them easily.
Missing solder
Solder improperly place on a circuit board pad can cause missing solder. Some inspection methods can eventually detect missing solder. However, x-ray images immediately detect the absence of solder.
Wrong placement of decoupling capacitors
Decoupling capacitors get rid of oscillation and transients. Also, they ensure power supply stability. Engineers connect these capacitors in parallel. Also, they place them close to components in contact with power supply. The wrong placement of capacitors can affect the performance of a device. PCB X-ray machine helps to detect the wrong placement of these capacitors.
Considerations for PCB X-ray Machine
There are several X-ray machines available out there. Also, these X-ray machines offer several features. Therefore, you should consider some features before choosing an X-ray machine.
Ease of use
The automation degree with already programmed inspections makes the whole operation easier. However, it is crucial the inspector understands the settings of the machine.
X-ray tube
The frequency of the use of the machine will determine the choice of X-ray tube. X-ray tubes are either closed tube or opened tube. Also, you can use open tube for short duration. However, closed tube is ideal for a long duration.
Maintenance cost
Several factors like the use of X-ray tubes and degree of automation determine maintenance cost. Also, the use of detectors and the selection of 2D or 3D system are crucial factors.
Filtered connector
The filtered connector helps to regulate the radiation exposure and corrects the whiteout image. Also, this helps to prevent increased exposure of X-rays on circuit board sample.
Why the X-ray Tube is Crucial in X-ray Inspection Device
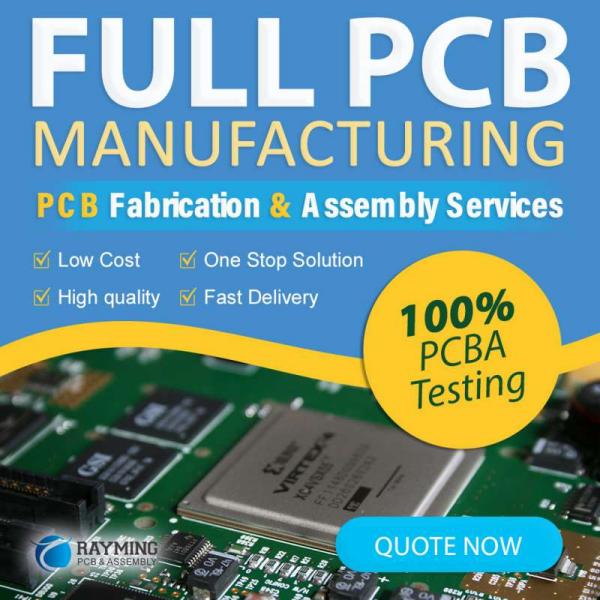
The X-ray tube is the most critical part of X-ray devices. Also, an X-ray tube is either closed tube or open tube. This tube is usually considered as the heart of the X-ray inspection devices. Without the X-ray tube, X-ray devices won’t function. Some elements determine the type of X-ray tube to opt for.
Open or closed tube
The X-ray tube type depends on the resolution of inspection devices. Higher resolution gives more delicate details. If the product is inspected at large scale, you can choose devices with any resolution. However, you will require a resolution of 2μm or below if CSPs and BGAs matter.
Target type
The target type can be reflective or penetrating. Also, the target type impacts the distance between X-ray tube and the sample.
X-ray power and voltage
The capability of the X-ray tube to penetrate is proportional to the voltage. With high voltage, the machine can inspect higher thickness and density. Also, you can choose X-ray inspection devices with low voltage if the inspected board is single-sided. However, high voltage is necessary if the inspected board is multi-layer.
Conclusion
X-ray inspection systems are crucial in PCB assembly and electronics manufacturing process. Also, the x-ray equipment is crucial for surface mount technology. BGA components are densely place on circuit boards. X-ray inspection penetrates small components and detects any error.
X-rays are becoming popularly used in industries for inspection of critical components. Also, X-ray inspection systems need to provide clear X-ray images that provide vital details during defect analysis. This inspection method has enhanced PCB and electronics production over the years.