- Perspective – March 2023
- Market Intelligence
- Columbus Advert
- State of the Stainless Steel Nation
- Webinar Report Back
- NDE Advert
- Demand Drivers
- PFERD-South Africa Advertorial
- Market Intelligence
- Fastenright Advert
- Case Study
- Passionate Professional Profile
- Member News
- Industry News
- Member Innovation
- Sassda News – Eastern Cape Golf Day
- Sassda News – Columbus Mill Visit
COULD STAINLESS STEEL HAVE SAVED THE LIBERTY SHIPS DURING WW2?
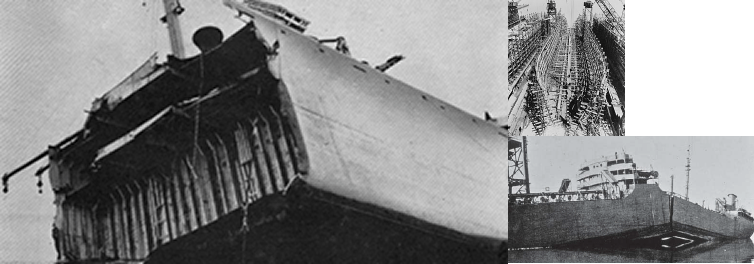
The Liberty Ship S.S. Schenectady, which, in 1943, failed before leaving the shipyard.
(Reprinted with permission of Earl R. Parker, Brittle Behavior of Engineering Structures, National Academy of Sciences, National Research Council, John Wiley & Sons, New York, 1957.)
By executive order of President Roosevelt, the United States started the production of all-welded cargo vessels (DWT 11000 Liberty Ships) in 1942 to meet the demands of the Pacific War. These cargo vessels were used as troop ships or carriers for large amounts of military logistics to ensure eventual US victory in the Pacific and were therefore named ‘Liberty Ships’.
The general aim was to build ships faster than the enemy could sink them. Nineteen pre-existing shipyards and eighteen newly built shipyards were set aside for the exclusive construction of the Liberty Ships. A total of 37 factories worked night and day on an assembly line to produce the Liberty Ships.
The use of welded structures instead of the more traditional riveted construction for a ship design enabled the fast continuous block manufacturing method. This manufacturing method of cargo ships was similar to that used in Japan during the same period. The scale involved in the Liberty Ship construction was astounding. Between 1939 and 1945, 37 shipyards produced 5 777 ships of which 2 708 were Liberty Ships.
Cracks in the system
The failure of many of the World War II Liberty Ships is a well-known and dramatic example of the brittle fracture of steel that was thought to be ductile. Some of the early ships experienced structural damage when cracks developed in their decks and hulls. Three of them catastrophically split in half when cracks formed, grew to critical lengths, and then rapidly propagated completely around the ships’ girths. The picture shown on the left is one of the ships that fractured the day after it was launched.
Subsequent investigations concluded one or more of the following factors contributed to each failure:
- The Liberty Ships were built of steel that experienced a ductile-to-brittle transition. When certain metal alloys, that are ductile at ambient temperatures, are cooled to relatively low temperatures, they become susceptible to brittle fracture. Some Liberty Ships were deployed to the frigid North Atlantic, where the once ductile metal experienced brittle fracture when temperatures dropped to below the transition temperature. This meant that their steel frame transformed from a ductile condition to a brittle condition upon cooling through a critical range of temperatures.
- The corner of each hatch was square; these corners acted as points of stress concentration where cracks could form.
- To deliver the fastest possible construction speed demanded by the war effort it became necessary to revolutionise construction methods. This was accomplished by using prefabricated steel sheets that were assembled by welding rather than by the traditional time-consuming riveting. Cracks in welded structures may propagate unimpeded for large distances and when structures are riveted, a crack ceases to propagate once it reaches the edge of a steel sheet.
- Weld defects and discontinuities where cracks could form were introduced by hastily trained and inexperienced welding operators.
Stainless could have saved the day
Could stainless steel have saved these vessels? The above lists of causes for the failure of these ships can be attributed to:
- The material selection did not consider all the factors in the operating environment and the mechanical properties of the selected steels in this environment.
- The design lacked basic engineering concepts relating to the avoidance of stress concentration at critical points in the structure of the ships.
- There was a lack of technical skills and technological competency amongst the workforce to address production and manufacturing challenges.
The lack of technical skills, suitable technology and processes, and design cannot be addressed by stainless steel, but it could have had an impact on the metallurgical reasons for the failures.
The ductile-to-brittle transition process that led to the failures was alloy and temperature range specific. It is also an indication of a material’s level of toughness in certain conditions. Toughness is the ability of a material to absorb energy when subjected to an impact load. This is explained by the graph showing the Ductile to Brittle Transition Temperature (DBTT) for a specific material.
At temperatures above (to the right of) the DBTT, the material is regarded as ductile, and the material will be tough. At these higher temperatures, the material will absorb elevated levels of energy during impact. As the material is cooled to temperatures lower (to the left) than the DBTT, the material loses its ability to absorb impact energy and becomes increasingly brittle and less tough.
This “S”- curve is characteristic of most metals. The point where the gradient switch on the “S” curve is then known as the DBTT with its correspondent energy absorbance. This means that virtually all metals would become brittle at some point during low external temperatures.
Austenitic stainless steel bucks the curve
There is an exception to this general rule. Austenitic stainless steel does not render a conventional curve on the DBTT graph, and the red line shows a typical austenitic curve. It is noticeable that the austenitic stainless steel grades do not exhibit the typical “S” curve, but only part of it.
This part of the “S” curve never reaches a low temperature where the gradient of the curve will change and, as such, does not have a DBTT. This means that austenitic stainless steel will remain ductile and tough even in cryogenic conditions at extremely low temperatures.
The answer to the question would then be technically yes. Stainless steel could have saved the ships that failed due to brittle failure. Austenitic materials were developed in the early part of the 1900s and would have been available during the second world war. However, this is easy to state in hindsight.
It should be remembered that at the time of the construction of the vessels, welding technology and material-making technology were not nearly as advanced as today. During the late 1930s and early 1940s stainless steel mills could produce the suitable grades for this application but did not have the technology to produce the required forms, i.e. the mills were not able to produce the large pieces of stainless steel materials with consistent metallurgical quality or flat products that could be used in the shipping industry.
The North American stainless steel mills could also not produce the quantity of material required. As mentioned, welding technology standards for stainless steel were also very different compared to the modern methods we currently employ. Most stainless steel welding was still based on brazing and soldering. Welding quality would have disqualified stainless steel as a replacement material.
We can conclude that stainless steel has been a solution to the world since its inception in 1913 for many a problem. Until recently we have never had a complete set of tools, skills, and knowledge to make full use of it. Who knows what the future holds for stainless steel, it is Simply Brilliant!